Analysis of Difficulties in Processing Medical Device Parts
by xiaolong luo cnc machining shopDifficult to process titanium alloy material
Ninety percent of medical device implants are made of Ti6Al-4V titanium alloy, which is derived from lightweight, high strength and high biocompatibility. Titanium 6AL-4V is the most commonly used material for medical implants. Titanium alloy 6AL-4V is commonly used in the manufacture of hip joints, bone screws, knee joints, bone plates, implants, and spinal connectors. Titanium alloys have work hardening properties. The machining process has a large shear angle, resulting in thin chips and a relatively small contact area on the tool. In addition, the high cutting force during the machining process, combined with the frictional force during the flow of the chips, will result in a partial high heat of cutting of the tool. The titanium alloy has poor thermal conductivity, so that the cutting heat cannot be conducted quickly. Thus, a large amount of cutting heat is concentrated on the cutting edge and the tool surface. High cutting forces and heat of cutting can cause the formation of craters and cause rapid tool failure.
The relatively low modulus of elasticity makes the titanium alloy more resilient to steel. Therefore, excessive cutting force should be avoided to ensure that the rebound of the workpiece is small. Thin-walled parts have a tendency to deform under tool pressure, causing chattering, friction and even tolerance problems. The key to solving the problem is to ensure the rigidity of the whole system. It is necessary to use sharp cutting edges and correct geometry. In addition, titanium alloys tend to be chemically alloyed with cutting tools at high temperatures, and their chips tend to be welded to the tool surface.
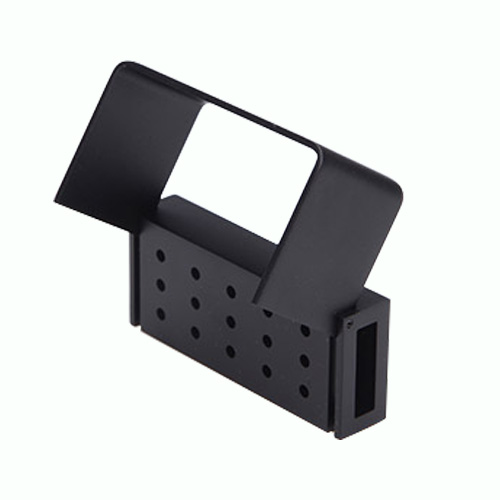
1. Reliable and compact machine tool fixture
Medical device processing equipment needs to be able to process small, complex parts made of difficult-to-machine materials (such as titanium or stainless steel) with high precision requirements, such as the replacement of bone and joint replacement parts. Due to the poor cutting performance of the machining material being processed, the blank is usually a bar stock - this means that a large amount of metal needs to be removed. As a result, some of the parts are cast close to the shape of the finished product, but this adds to the hassle - the need to make complex and expensive fixtures. Another factor that increases processing complexity is the narrow tolerance range.
The requirements for workpiece materials, processing precision, and surface finish of medical device parts are high, which requires high reliability of the processing system. As a result, extremely high demands are placed on machine tools, fixtures, tools, and CAM software. Workpieces are typically machined on advanced medical equipment processing equipment such as Swiss automatic lathes, multi-spindle machines and rotary tables. The characteristics of these machines are mostly very small in size and very compact in structure.
The characteristics and requirements of medical device parts processing have undoubtedly promoted the development of processing technology and solutions to improve the competitiveness and production efficiency of medical devices processed by small and medium-sized enterprises.
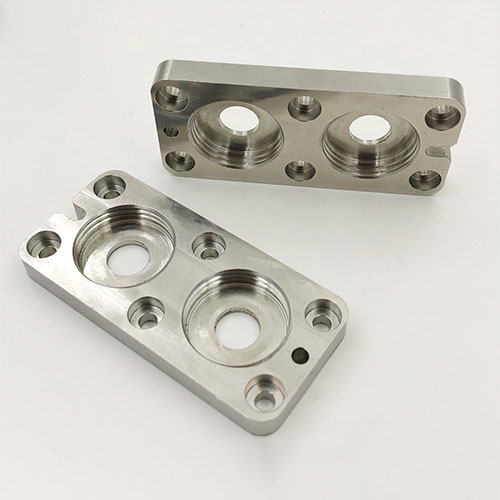
2. Stable and efficient tool
In general, the medical device industry differs from other machining industries in three ways:
First, the requirements for machine tools are relatively high. Advanced medical equipment processing equipment such as Swiss automatic lathes, multi-spindle machines and rotary tables are completely different from the usual machining centers and lathes. They are very small in size and very compact. In response to such requirements, the structure of the tool also requires a special design, requiring the size of the tool to be small, while also ensuring the rigidity of the tool. Like the Iss SWISSCUT series, which is specially designed for cam-type machine tools, it reduces the problem of small interference in the processing area. It can be easily replaced from both sides of the holder. High-precision blades and a strong holder design ensure high height. Repeatability. MINCUT is Isa's newly developed tool for both turning and milling. Small-size tools are highly rigid and can be used on multi-spindle machines or machining centers.
Second, the processing efficiency is high. For medical devices, the most important thing is the processing efficiency, that is, the processing cycle, which requires the blade to be replaced in the shortest time. Iskar's MULTI-MASTER Transformer replaceable cutter head series can be replaced with different milling heads in just a few seconds. The concept of quick change of the cutter head has a good guarantee for the processing beat. In addition, the life of the tool is required to be as stable as possible and as long as possible. High-quality tools should be used as much as possible, with the overall fit of coating, cutting edge, chipbreaker and tool structure. In this way, the machine can be operated 24 hours a day to compete with other competitors on the market with very high production efficiency, thus achieving a competitive advantage.
Third, from the workpiece itself, it is very different from other mechanical components. Medical machining devices implanted in the human body first require a very good surface finish with very high precision and no deviation. This requires the tool to meet the high processing requirements from the design of the blade structure to the design of the blade coating. In addition, it also includes the repeatability of the blade, which ensures high efficiency while not neglecting high quality requirements.
3. Complete solution
PTJ Shop provides an in-depth analysis of the characteristics of implants in the medical device industry to improve the processability of these very critical components. Therefore, PTJ Shop also designs special tools, inserts and chip flutes to process titanium Ti6Al4V and achieve the high precision tolerances required for this particular field. To match the manufacturer's existing production equipment, Iskar also offers special tools to suit different applications.
PTJ's solid carbide end mills with sharp cutting edges can be used for the machining of concave parts without burrs. These end mills are capable of polishing and milling up to 0.01 mm in semi-finishing and finishing. We also develop tools for the simultaneous processing of titanium alloys and stainless steels - PVD coatings based on ultra-fine grain substrates for high cutting speeds and high feed rates. The milling cutter has a small diameter and can be used in the programming process. The advantage is that the cutting speed on the outer diameter of the tool can be obtained, the chip removal is smooth, and the cutting heat is lower under the contact area of the cutting area.
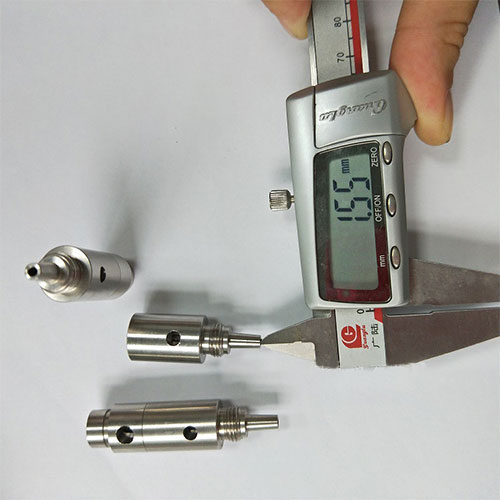
The R&D department of PTJ Shop found that turning applications in the medical device industry require improvements in the number of inserts or the chip flutes. In order to meet the needs of users, Iskar has developed high-quality ground blades, such as VCET, DCET, CCET, etc., and the insert groove type is WF. Iskar's advanced production technology guarantees the improved blade with polished coil pockets for superior surface quality in semi-finishing and finishing. In some special applications, Iska offers VCGT inserts with MD coils for high surface quality. PTJ Shop's JET-CUT series of cutting knives with blade widths of 3mm and 4mm, high surface quality and long tool life. From Isa's belief that there is no limit to the upgrade, PTJ Shop has developed HP high pressure cooling system tools based on the TANG-GRIP series.
The use of proven processes and tools and proven cutting parameters allows for more timely delivery of medical device parts and components. Based on years of experience in the medical device industry, PTJ Shop has also introduced tool sets for the medical device industry, in conjunction with DMG machines, to provide turnkey projects for customers.
PTJ Shop has seen the huge development prospects of medical machinery, and invested a lot of manpower and material resources to develop special tools for medical device processing. PTJ Shop has established a dedicated medical device R&D department at its headquarters. Seven professional engineers are involved in the design of the program. They have extensive experience and have been engaged in the research of medical device processing tools for more than 12 years.
At present, the proportion of tools used in the medical device industry in PTJ Shop processing products is about 6% to 7%. It is expected that this proportion will rise to 10% to 12% in the next two to three years.
Sponsor Ads
Created on Nov 4th 2019 20:31. Viewed 397 times.
Comments
No comment, be the first to comment.