Syngas Contaminant Removal and Conditioning | Coal Gasification Encyclopedia
by Rudy P. SysAdmin at howtofindthemoneyRaw synthesis gas (syngas) from the high temperature gas cooling (HTGC) system needs to be cleaned to remove contaminants including fine particulates, sulfur, ammonia, chlorides, mercury, and other trace heavy metals to meet environmental emission regulations, as well as to protect downstream processes. In the case of carbon sequestration, carbon dioxide (CO2) is also removed. Depending on the application, syngas may need to be conditioned to adjust the hydrogen-to-carbon monoxide (H2-to-CO) ratio to meet downstream process requirement. In applications where very low sulfur (<10 ppmv) syngas is required, converting carbonyl sulfide (COS) to hydrogen sulfide (H2S) before sulfur removal may also be needed. Typical cleanup and conditioning processes include cyclone and filters for bulk particulates removal; wet scrubbing to remove fine particulates, ammonia and chlorides; solid absorbents for mercury and trace heavy metal removal; water gas shift (WGS) for H2-to-CO ratio adjustment; catalytic hydrolysis for converting COS to H2S; and acid gas removal (AGR) for extracting sulfur-bearing gases and CO2 removal.
Fine Particulate Removal
Raw syngas leaving the HTGC system in today's commercial gasification plant is normally quenched and scrubbed with water in a trayed column for fine char and ash particulate removal prior to recycle to the slurry-fed gasifiers. For dry feed gasification, cyclones and candle filters are used to recover most of the fine particulate for recycle to the gasifiers before final cleanup with water quenching and scrubbing. In addition, fine particulates, chlorides, ammonia, some H2S, and other trace contaminants are also removed from the syngas during the scrubbing process. The scrubbed gas is then either reheated for COS hydrolysis and/or a sour WGS when required, or cooled in the low temperature gas cooling (LTGC) system by generating low pressure steam, preheating boiler feed water, and heat exchanging it against cooling water before further processing.
Spent water from the scrubber column is directed to the sour water treatment system, where it is depressurized and decanted in a gravity settler to remove fine particulates. Solid-concentrated underflows from the settler bottom are filtered to recover the fine particulate as the filter cake, which is then either discarded or recycled to the gasifier depending on its carbon content. Water from the settler is recycled for gasification uses with the excess being sent to the wastewater treatment system for disposal.
Mercury and Trace Elements
Current commercial practice is to pass cooled syngas from LTGC through sulfided, activated carbon beds to remove over 90% of the mercury and a significant amount of other heavy metal contaminants. Due to the sulfur in the activated carbon, these beds are normally placed ahead of the AGR system to minimize the possibility of sulfur slipping back into and contaminating the cleaned syngas.
Newer regulations are demanding increased levels of mercury reduction as well as that of other toxic species present in syngas, which may require increasing sophistication in technology to remove these contaminants.
ACID GAS REMOVAL (AGR)
Operation
Acid gases produced in gasification processes mainly consist of hydrogen sulfide (H2S), carbonyl sulfide (COS), and carbon dioxide (CO2). Syngas exiting the particulate removal and gas conditioning systems, typically near ambient temperature at 100°F, needs to be cleaned of the sulfur-bearing acid gases to meet either environmental emissions regulations, or to protect downstream catalysts for chemical processing applications. For integrated gasification combined cycle (IGCC) applications, environmental regulations require that the sulfur content of the product syngas be reduced to less than 30 parts per million by volume (ppmv) in order to meet the stack gas emission target of less than 4 ppmv sulfur dioxide (SO2)1. In IGCC applications, where selective catalytic reduction (SCR) is required to lower NOx emissions to less than 10 ppmv, syngas sulfur content may have to be lowered to 10 to 20 ppmv in order to prevent ammonium bisulfate fouling of the heat recovery steam generator's (HRSG) cold end tubes. For fuels production or chemical production, the downstream synthesis catalyst sulfur tolerance dictates the sulfur removal level, which can be less than 0.1 ppmv.
Conventional processes for removing acid gases typically involve their countercurrent absorption from the syngas using a regenerative solvent in an absorber column. This process approach of gas-liquid contacting to remove acid gases is very commonly used in a wide range of process industries, including refining, chemicals, and natural gas production. However, because of the significantly different required degrees of acid gas removal that depend on the application, the choice of solvents varies significantly:
- For chemical synthesis applications which require syngas with less than 1 ppmv sulfur, physical solvent processes such as Rectisol and Selexol are normally used which allow essentially total removal of sulfur; these may operate at depressed temperatures (Rectisol operates at -40°C).
- For power generation applications, which allow higher sulfur levels (approximately 10 to 30 ppmv sulfur), chemical solvent processes such as Methyl diethanolamine (MDEA) are normally used. Many but not all of these utilize amine-type solvents.
- Mixtures of chemical and physical solvents, also known as hybrid or composite solvents are also possible; Sulfinol is a well-known example.
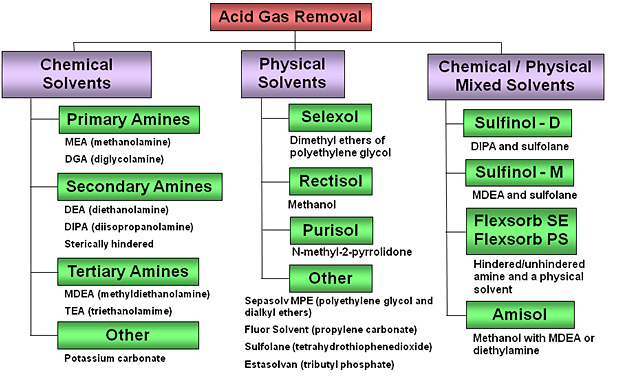
Acid Gas Removal Technologies
In both physical and chemical absorption processes, the syngas is washed with lean solvent in the absorber to remove H2S. Cleaned syngas is sent to downstream systems for further processing. Acid gas-rich solvent leaving the bottom of the absorber is sent to the regenerator, where the solvent is stripped with steam under low pressure (reboiling) to remove the absorbed sulfur. The concentrated acid gas stream, rich in H2S, exits the top of the regenerator and is sent to the Sulfur Recovery Unit (SRU) for sulfur recovery. The SRU consists of a Claus plant, in which the H2S is converted to sulfur, a salable byproduct. The regenerated lean solvent from the bottom of the regenerator is cooled by a heat exchanger against the rich solvent, followed by water cooling before being recycled back to the top of the absorber to start the absorption process cycle again.
The physical solvent processes tend to co-absorb more CO2 than chemical/amine processes such as MDEA. Multiple step depressurization of the rich solvent, supplemented with nitrogen stripping, is employed by the physical solvent processes to reject sufficient CO2 to concentrate the acid gas from the regenerator overhead to at least 15 to 25 volume% H2S in order to feed the Claus SRU.
Because of the need for refrigeration (e.g. Rectisol), and in general more complex solution flashing arrangements, physical solvent processes are two to three times more costly than chemical solvent processes. While the physical solvent processes have higher power consumption than the chemical solvent processes, the chemical processes have higher steam consumption which translates to reduced power output from the power train. Thus, impact on overall net power output may be similar between the two types of AGR processes.
Depending on the solvent used, COS may first need to be converted to H2S via a COS hydrolysis unit. Also, it is important to note that H2S and CO2 can be removed either simultaneously or selectively, depending on the raw syngas composition and conditions, and the end syngas specifications.
Chemical Solvents
Chemical solvents include primary, secondary and tertiary amines, and alkaline salts such as potassium carbonate. Through acid-base reactions, aqueous solutions of these basic compounds capture and remove acid gases by forming weak chemical bonds with dissolved acid gases in the absorber. The bonds are broken by heat in the regenerator to release the acid gases and regenerate the solvent for reuse. Chemical solvent absorption processes normally operate at slightly above ambient temperature. Chemical solvents are more effective for low acid gas partial pressure applications than physical solvents.
Physical Solvents
Physical solvents are organic solvents that have a high affinity for acid gases. In general, the physical solvents demand relatively high syngas pressures, high partial pressure of the acid gases, and/or low operating temperature in the absorber (in some cases cryogenic temperatures below –150°C, –238°F or 123 K), for good performance. Solvent, rich with acid gases from the absorber, is then subjected to multistage controlled pressure decreases, followed with hot stripping in the regenerator, to release the acid gases and regenerate the solvent for reuse.
Mixed Solvent Systems
Mixtures of amine chemical solvents and physical solvents take advantage of the high treated-gas purity performance of chemical solvents, and the low energy requirement associated with flash regeneration of physical solvents. In general, such mixtures are effective over a wide range of acid gas partial pressures at near-room temperatures, allowing both improved acid gas absorption at high partial pressures, and with the amine portion allowing AGR under very low partial pressures as the case may be. Also, they feature higher solubility of COS and organic sulfur compounds than aqueous amines alone.
Applications
There are over 30 AGR processes available commercially, but only four of these have been demonstrated or implemented in the 18 commercial-size coke or coal-based gasification plants worldwide, as reported by SFA Pacific in 2002:2 Rectisol, Selexol, Sulfinol, and MDEA. Half of these18 plants are for liquid fuels, methanol, SNG or ammonia production, while the other half are IGCC applications.
Eight of the nine chemical production plants, in operation as of 2002, use Rectisol (typically operates at -40°F to -80°F), and one uses Selexol (typically operates at 20°F to 40°F). This is consistent with the general perception that physical solvent-based AGR is normally selected to protect synthesis catalysts against poisoning from sulfur and other trace contaminants in chemical production from coal applications. While Rectisol is more costly, it is preferred for treating coal-based syngas because it allows for very deep sulfur removal (<0.1 ppmv H2S plus COS), and also because it can remove HCN, NH3, and many metallic trace contaminants (including iron- and nickel-carbonyls, and mercury) to provide additional catalyst protection.
SULFUR RECOVERY AND TAIL GAS TREATING
Sulfur is a component of coal and other gasification feed stocks. Resulting sulfur compounds in syngas need to be removed in most gasification applications due to environmental regulations or to avoid catalyst poisoning. Whether it is electricity, liquid fuels, or some other product being output, sulfur emissions are regulated, and sulfur removal is important for this reason, along with the prevention of downstream component fouling. In addition to these constraints, recovering saleable sulfur is an important economic benefit for a gasification plant.
To illustrate the previous point, in 2011 8.1 million tons of elemental sulfur was produced, with the majority of this coming from petroleum refining, natural gas processing and coking plants. Total shipments were valued at $1.6 billion, with the average mine or plant price of $200 per ton, up from $70.48 in 2010. Prices have fluctuated in recent years, but price of sulfur in 2014 has still been well over $150 per ton. The United States currently imports sulfur (36% of consumption, mostly from Canada), meaning the market can support more domestic sulfur production.
USGS Mineral Commodity Information: Sulfur
In a typical design, a series of process steps is used to recover sulfur as a useful by-product from gasification processes. First, cooled syngas/feed gas is contacted with a chemical solvent in an absorber unit, where, as the gas passes through, almost all of the hydrogen sulfide (H2S) and some carbon dioxide (CO2) are removed in the basic acid gas removal (AGR) process. The solvent is now rich with H2S and it moves on to a stripping unit to clean and recycle the solvent and separate the H2S. The basic stripping process and solvent stripping/regeneration are depicted below.
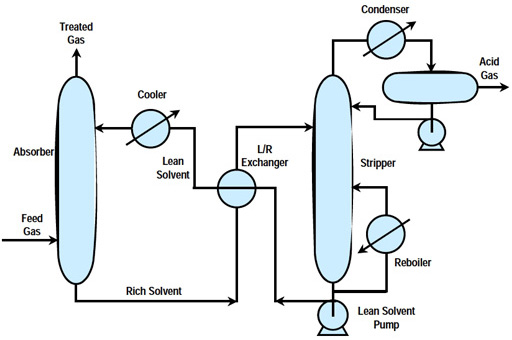
Simplified Diagram of the AGR Process
The sulfur-containing acid gases removed by the AGR process consist primarily of a mixture of hydrogen sulfide (H2S) and carbon dioxide, which is inevitably captured along with the H2S to some degree. This serves as feed gas to a sulfur recovery process, in which sulfur is recovered as either liquid or solid elemental sulfur, or as sulfuric acid, depending on market demands. For an elemental sulfur product, a Claus sulfur recovery unit produces elemental sulfur from H2S in a series of thermal stage followed by multiple catalytic stages, achieving about 98% recovery of the sulfur in the syngas. Part of the H2S is oxidized to produce sulfur dioxide (SO2), which is then reacted with the remaining H2S to give elemental sulfur and water. Tail gas from the Claus process is sent for further treatment to a Tail Gas Unit (TGU), which may be exemplified by the amine-based Shell Claus Off-gas Treatment (SCOT) unit. The SCOT unit removes nearly all of the remaining sulfur—in the form of a tail-gas stream of unreacted sulfur, H2S, SO2, and carbonyl sulfide (COS)—that the Claus unit misses. The SCOT unit uses a cobalt-molybdenum catalyst to convert SO2 to H2S, which is then removed in an absorber. Altogether, this process series approach can achieve a typical overall sulfur recovery of 99.8%.
Sulfuric acid synthesis is an alternative to sulfur recovery via the Claus process. This may be preferred if the plant is located close to a sizeable market for sulfuric acid. In this case, H2S is first burned in a furnace to form SO2, which is then converted to sulfur trioxide (SO3), which is then scrubbed with water or a recycled weak sulfuric acid stream to yield saleable 98% sulfuric acid. Typically, 99.8% of the H2S can be recovered in a sulfuric acid plant.
PARTICULATE REMOVAL
Background
Particulate matter (PM) consists of microscopic solid particles or liquid droplets which are small enough to enter the lungs and cause health problems. Both nitrogen oxides (NOx) and sulfur oxides (SOx) are associated with the formation of particulate matter, but other processes can contribute to their formation. Aside from health concerns, particulates cause reduced visibility and haze when released in the atmosphere.
Ash is formed in coal combustion and gasification from inorganic impurities in the coal. Some of these impurities react to form microscopic solids which can be suspended in the exhaust gases in the case of combustion, or the syngas produced by gasification. In the latter case, raw syngas leaving the gasifier contains fine ash and/or slag that needs to be removed prior to sending the gas downstream for further processing. The bulk of the particulates are removed using dry particulate removal systems such as filters and/or cyclones. High temperature ceramic filters have been developed for gasification applications and are currently commercially available. The recovered fly ash/slag can either be recycled to the gasifier or purged from the system as a byproduct. The syngas leaving the dry particulate removal system is then further purified by passing through a wet scrubber where any residual solids can be removed down to a 1 ppm level.
Gasification offers two main advantages in particulate control over combustion processes. First, gasification of coal provides the capability of removing most of the ash as inert slag or bottom ash for disposal or sale as a byproduct. Second, since the syngas leaving the gasifiers is much more dense than combustion exhaust gases, the particulate matter can more easily be removed. The following figure gives an indication of the advantage that gasification has for particulate emissions.
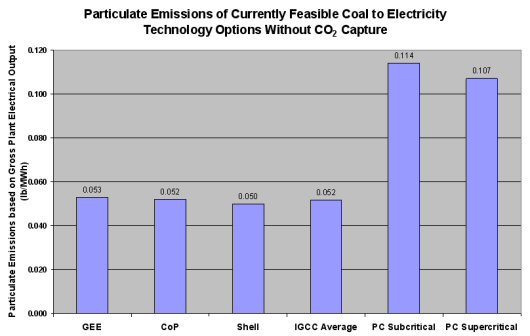
Dry Particulate Removal
Bulk solid particulate removal can be achieved with either filters and/or cyclones, depending on the gasification system and operating conditions. Cyclones are a commercially proven technology and can be refractory-lined for high temperature operations. High temperature candle filters have been developed and can remove particulates from raw syngas at temperatures between 550°F and 900°F (~ 300°C to 500°C). Below 550°F, the filters may be blinded by deposits of ammonium chloride. Above 900°F, alkali compounds may pass through the filters at unacceptable levels, as the vapor pressures of these compounds may still be high. Development of candle filters that can remove particulates at high temperatures is a significant technology development for gasification. Use of candle filters in dry solids removal systems is now considered commercially available technology. In some current gasification designs, candle filters are being used upstream of a wet scrubber for effective overall solids removal.
Effective dry particulate removal is an integral part of the warm gas cleanup (WGCU) technology development effort being undertaken by Research Triangle Institute (RTI) with funding from the Department of Energy (DOE).
Wet Scrubbing
In most commercial gasification operations, syngas leaving the filter is quenched and scrubbed with water for final particulate removal. Water scrubbing takes place below the dew point temperature of the syngas so that the finest solid particles can act as nuclei for condensation, thus ensuring that all solids can be removed efficiently. Scrubbing also removes chlorides, ammonia, some hydrogen sulfide (H2S) and other trace contaminants from the syngas. Typically, the scrubbed syngas is reheated for carbonyl sulfide (COS) hydrolysis and/or a sour water gas shift (WGS) if required, followed by cooling in a low temperature gas cooling (LTGC) system to generate low pressure steam. After these processes, the syngas is sent downstream for sulfur and mercury removal.
Spent water from the scrubber column is directed to a gray water treatment system where it is depressurized and vacuum flashed. The spent water is then decanted into a gravity settler to remove particulates. Solid-concentrated underflows from the settler bottom are filtered to recover the fine particulate as a filter cake, which is then either discarded or recycled to the gasifier depending on its carbon content. Water from the settler is recycled for gasification reuse, with excess being sent to the wastewater treatment system for disposal.
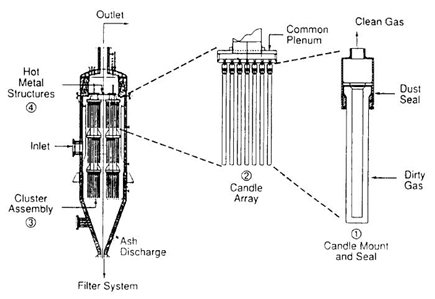
Candle Filter System

Candle Filter Element
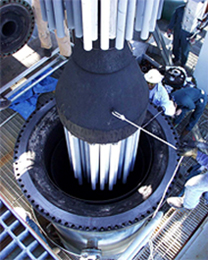
Picture of a Candle Filter System
Regulatory Constraints on PM at Edwardsport IGCC
Current regulations on filterable PM from new IGCC units set the limit at 0.07 lb/MHh (syngas + syngas duct firing) and 0.09 lb/MWh (syngas + natural gas duct firing). Edwardsport is 0.019 lb/MMBtu;1 with heat rate of 4,218 MMBtu/hr this is equivalent to a limit of 80.1 lb/h. Actual emissions of PM/PM10/PM2.5 at Edwardsport are estimated to be 36.0 lb/h with SCR engaged and 39.1 lb/h with SCR disengaged, both well under the limit.
MERCURY/TOXICS EMISSIONS
Overview
Assessment of the environmental performance of coal-based integrated gasification combined cycle (IGCC) technology indicates that vapor-phase mercury (Hg) emissions may need to be further reduced to comply with future U.S Environmental Protection Agency (EPA) mercury regulations. The purpose of this section is to examine both commercial and near-commercial methods for integrating such control into a typical IGCC system.
Two basic approaches for control are: 1) turbine exhaust gas treatment and 2) syngas treatment. While vapor-phase mercury can potentially be removed from the flue gas exiting the gas turbine/heat recovery steam generator (HRSG), it is more effective in IGCC systems to remove Hg from the syngas prior to combustion. This may already occur, to some extent, via the acid gas scrubbing system, but more data are required to verify this. Syngas removal has the advantage of higher mercury concentration, lower mass flow rates, and higher pressure than the stack gas. Disadvantages include operation in a reducing environment (more corrosive environment), possible operation at a high temperature if part of a hot gas cleanup system, possible presence of other contaminants, and greater safety issues related to premature combustion. A review of syngas control options revealed that several commercially available technologies, using sorbents such as activated carbon, have already been successfully applied to gasification applications, as well as other gaseous hydrocarbon streams. These are discussed below.
UOP Corporation has a commercial product that is in wide use in natural gas/natural gas liquids and LNG (liquefied natural gas) plants called HgSIV. It is a molecular sieve (MS) that removes very low levels of elemental mercury from natural gas or syngas via a regenerable adsorption process. It uses a 2-bed thermal-swing MS adsorption system. The gas flows through one adsorbent bed to adsorb Hg, while the temperature of the other bed rises to desorb Hg. After regeneration, the beds are reversed. Hg removal is needed in NGL or LNG plants to protect the braised aluminum heat exchangers in the cryogenic section from mercury attack. HgSIV has been successfully operated in about 30 plants for almost 10 years1.
Eastman Chemical Company has developed and successfully applied activated carbon-based mercury control technology at their Chemicals from Coal Facility located in Kingsport, Tennessee2. Eastman has been operating GE Energy (formerly ChevronTexaco gasifiers) at this facility since 1983 to provide syngas for the production of acetyl chemicals. They utilize Calgon’s HGR-P sulfur-impregnated, pelleted activated carbon beds with the following performance characteristics:
- Operating conditions: Approximately 30°C (86°F) and 900 psi
- Gas contact time in bed: Approximately 20 seconds (based on total packed volume)
- Removal efficiency: Ranges from 90-95%
- Carbon lifetime: 12 to 18 months based on a buildup in pressure drop, a buildup in water in the bed, or a buildup of other contaminants.
Eastman Chemical operates their carbon beds ahead of the sulfur recovery unit. The use of dual beds, (i.e., two beds in series) should be capable of achieving carbon removal levels of greater than 99%.
Sorbents for Mercury Capture
A number of companies produce activated carbons that have been used commercially for mercury removal from combustion flue gas, with most of the applications being for incinerator stack gas. Norit’s DARCO® Hg series of lignite-derived activated carbons are manufactured specifically for the removal of heavy metals and other contaminants typically found in utility flue gas3. It has been proven in numerous full-scale facilities to be highly effective for the removal of gaseous mercury, dioxins (PCDD) and furans (PCDF). Its open pore structure and fine particle size permit rapid adsorption, which is critical for high performance in gas streams where contact times are short. It is a free flowing powdered carbon with minimal caking tendencies that makes it appropriate for automatic wet or dry injection systems. It has a very high ignition temperature, which permits safe operation at the elevated temperatures inherent in incinerator flue gas. This material has also been successfully used in a number of R&D programs focused on evaluation of mercury removal from coal-fired power plant stack gas.
UOP has developed several commercial mercury sorbents, including the copper on alumina GB adsorbents, and a line of zeolite-based desiccants called HgSIV modified with silver for enhanced mercury removal capability. Zeolites are crystalline structures not unlike sponges on a molecular scale. They have a solid framework defining large internal cavities where molecules can be adsorbed. These cavities are interconnected by pore openings through which molecules can pass. Because of their crystalline nature, the pores and cavities are all precisely the same size, and depending on the size of the openings, they can adsorb molecules readily, slowly, or not at all, thus functioning as molecular sieves -- adsorbing molecules of certain sizes while rejecting larger ones. UOP indicates that their HgSIV products have proven to be reliable in removing mercury from natural gas, natural gas liquids, and other process streams such as ethylene4.
Calgon Carbon’s family of FluePac® powdered activated carbons is specially manufactured for use in flue gas treatment5. Their high effective surface area and large pore volume make them extremely effective in removing common contaminants, including mercury, dioxins, furans, and volatile organic compounds (VOCs). Typical applications include municipal waste combustors, hazardous waste combustors, hospital waste incinerators, coal-fired power plants, cement kilns, and industrial boilers. These coal-derived powdered activated carbons have a high minimum Iodine Number (measurement of available surface area) with up to twice the amount of high-energy adsorption sites compared to other adsorbent carbons. With proper dosing levels, Calgon claims that over 95 percent reduction in mercury/dioxin is achievable. This sorbent has been used by Eastman Chemical Company in their gasification facility to control mercury.
Use of these sorbents for mercury control may also provide the added side benefit of residual hydrogen sulfide (H2S) removal, which could improve IGCC integration with add-on nitrogen oxides (NOx) control technologies such as selective catalytic reduction (SCR). However, their effectiveness for this purpose has to be verified.
Cost of Mercury Control Based on Activated Carbon Adsorption
NETL’s own cost and performance baselines for IGCC plant configurations provide information on cost of mercury control in this context. As an example, the bituminous coal to electricity IGCC cases assume that activated carbon beds would be used, with performance data derived from the experience of Eastman Chemical Company’s syngas facility in Kingsport, Tennessee as discussed previously. Assumptions were Illinois #6 coal with 0.15 ppm dry mercury content, packed carbon bed vessels (Calgon carbon) located upstream of the sulfur recovery unit, with syngas entering the beds at a temperature near 38°C (100°F), carbon bed removal efficiency of 95 percent, which would meet targeted emissions levels (actual emissions would be 4.16 x 10-6 lb/MWh, considerably less than the NSPS limit of 20 x 10-6 lb/MWh), and gas velocity, carbon replacement frequency, and other process parameters mirroring the practices at the Eastman syngas facility. For a GE Energy gasifier-based IGCC plant producing net power of 622 MWe without carbon capture, total plant capital cost for the mercury removal system is estimated to be $2,561,000 or $4.11/kW. Initial activated carbon cost is $58,000 with annual replenishment cost of ~$23,000 assuming a $1.05/lb cost of the carbon, while disposal cost of the hazardous spent carbon sorbent is ~$9,000 per year.
New Emissions Limits on Mercury and Air Toxics
Subsequent to the release of the NETL baselines, stringent regulations have been enacted for trace contaminant emissions from IGCC systems. Specifically, the U.S. Environmental Protection Agency’s (EPA) December 21, 2011, Mercury and Air Toxics Standards (MATS), the first national standards for mercury (Hg) pollution from power plants, require existing power plants to reduce Hg pollution by 90%, reduce acidic gases (hydrogen chloride [HCl] and hydrogen fluoride [HF]) by 88%, and substantially reduce other pollutants by 2015.6 Moreover, MATS requires new/in-construction power plants to conform to even higher standards of upwards of 99.9%. These have been officially reconsidered, with EPA issuing a notice of final action on reconsideration on March 28, 2013. In June 2013 40 CFR Parts 60 and 63 were published in the Federal Register, which finalized reconsideration of all the issues included in the proposed rule except those related to facilities startup and shutdown, with the EPA reopening the public comment period for the proposed reconsideration to solicit additional input on startup and shutdown and to request comment on the additional technical analyses it conducted.7 EPA has reported that implementation to meet proposed revised standards will be essentially the same as that which would have been chosen in complying with the original MATS rule.8 The U.S. Department of Energy (DOE) targets for trace contaminant removals are also stringent in order to avoid poisoning: (1) the catalysts essential for making liquids from fuel gas, (2) the electrodes in fuel cells, and (3) the selective catalytic reduction (SCR) catalysts employed in coal- or gas-burning power plants.
The EPA MATS requirement for Hg emissions of new IGCC-based power plants is 3 x 10-6 lb/MWh gross power output (~2 ppbw). This is considerably more stringent than the former NSPS limit of 20 x 10-6lb/MWh to which the NETL baselines were ascribing. However, those baselines also assumed 95% mercury removal, which brought their actual Hg emission rates into the 4 to 5 x 10-6 lb range, nearly meeting the new MATS requirements, while recovery of mercury to 99% would still be possible with activated carbon; the higher recovery percentage would bring the emissions rates well under the MATS limits.
Mercury Control in High Temperature Syngas Cleanup
Capture of Hg and other trace metal/toxic contaminants (arsenic [As], selenium [Se], cadmium [Cd], antimony [Sb], and phosphorus [P]) in syngas is optimal at lower temperatures; the types of carbon sorbents in the foregoing discussion are generally intended for utilization in near-ambient temperature removal of Hg from natural gas and syngas and for removal of Hg from flue gas at temperatures up to 350°F.9,10,11,12,13,14,15 However, these sorbents have been reported to be unsatisfactory for Hg removal at temperatures exceeding 400°F.16,17,18 In fact, few sorbents have been shown to remove Hg from high-temperature syngas because: 1) the physical adsorption of Hg on a sorbent typically decreases with increasing temperature; 2) Hg compounds formed on the surface of a sorbent can thermally decompose or desorb at high temperatures; and 3) chemical promoters, such as sulfur or halogens, will desorb from the sorbent at elevated temperatures. In addition to these problems, carbon-based sorbents lack the desirable chemical resistance and regeneration capability properties for warm-gas cleanup (WGCU).19
Unfortunately, the limitations of current sorption technologies based on activated carbons are at odds with efforts to develop and implement high-temperature, or WGCU of syngas, which would boost the thermal efficiency of IGCC plants. WGCU would have the additional benefits of removing toxic contaminants from warm syngas nearer the gasifier exit, helping to eliminate the circulation of dirty water and treatment systems downstream in IGCC plants; reducing the footprint, cost, and complexity of the systems; and ensuring the disposition of trace metal pollutants so that they will not contaminate process equipment, poison raw materials, or foul catalysts or fuel cells.20,21,22,23 Accordingly, the identification and development of a durable sorbent material capable of effectively and efficiently removing Hg and other trace metals at both elevated temperatures and pressures characteristic of actual process conditions have been a high priority.
Drawing on previous experience with sorbents in coal combustion flue gas, NETL has selected potential high-temperature candidate sorbents, developed a process for testing the various candidate sorbents at bench-scale in simulated WGCU, and determined the capacities of the sorbents for capture of Hg, As, Se, and P. Palladium (Pd)-based sorbents are currently among the most promising candidates, as they have been found to effectively capture trace contaminants such as Hg, As, Se, and P from syngas at elevated temperatures (400 to 700°F).24 The sorbents are described in U.S. patent 7,033,419, issued in April 2006. A license agreement between NETL and Johnson Matthey (JM) for further research, development, and commercialization of the sorbents for application in IGCC and in chemicals production from syngas was signed in March 2007. Collaboration between JM and NETL resulted in thorough characterization and bench-scale tests of these Pd sorbents,25,26,27 including testing of the sorbent in slipstreams of dirty fuel gas that began in 2009. More recent tests of the technology at larger-scale have taken place at Southern Company’s Power Systems Development Facility at the National Carbon Capture Center. Results have been highly promising, with more than 99% removal of Hg, As, and Se from dirty fuel gas slipstreams at 550°F over long periods (several weeks).
COS HYDROLYSIS
Most of the sulfur in the coal is converted to hydrogen sulfide (H2S) during gasification. However, depending on the gasification temperature and moisture content, approximately 3 to 10% of the sulfur is converted to carbonyl sulfide (COS). In applications where very low sulfur (< 10 ppmv) syngas is required, converting COS to H2S before sulfur removal may be necessary, because most current commercial AGR processes do not efficiently remove sulfur in the form of COS. This is done by passing syngas from the water scrubber through a catalytic hydrolysis reactor where over 99% of the COS is converted to H2S according to the following reaction:
COS + H2O ↔ H2S + CO2
The scrubbed syngas feed is normally reheated to 30-50°F above saturation before entering the reactor to avoid catalyst damage by liquid water. COS hydrolysis uses an activated alumina-based catalyst, and is normally designed to operate at 350°F to 400°F. The reaction is largely independent of pressure. The equilibrium for COS conversion is favorable at low temperatures due to the exothermic nature of the reaction; however, the heat of reaction is normally dissipated throughout a large amount of non-reacting components, yielding nearly isothermal reactor conditions.
COS hydrolysis product gas is cooled in the LTGC system by generating low pressure steam, preheating boiler feed water, and heat exchanging against cooling water before going through the acid gas removal system for sulfur removal.
WATER GAS SHIFT & HYDROGEN PRODUCTION
Water Gas Shift
In applications where scrubbed syngas hydrogen/carbon monoxide (H2/CO) ratio must be increased/adjusted to meet downstream process requirements, the syngas is passed through a multi-stage, fixed-bed reactor containing shift catalysts to convert CO and water into additional H2 and carbon dioxide (CO2) according to the following reaction known as the water-gas shift (WGS) reaction:
CO + H2O ↔ H2 + CO2
The shift reaction will operate with a variety of catalysts between 400°F and 900°F. The reaction does not change molar totals and therefore the effect of pressure on the reaction is minimal. However, the equilibrium for H2 production is favored by high moisture content and low temperature for the exothermic reaction. Normally, excess moisture is present in the scrubber syngas from slurry-fed gasifiers sufficient to drive the shift reaction to achieve the required H2-to-CO ratio. Indeed, for some slurry-fed gasification systems, a portion of the syngas feed may need to be bypassed around the sour shift reactor to avoid exceeding the required product H2-to-CO ratio. On the other hand, additional steam injection before the shift may be needed for syngas output by dry-fed gasifiers.
In any case, the scrubber syngas feed is normally reheated to 30 to 50°F above saturation temperature to avoid catalyst damage by condensation of liquid water in the shift reactor. Shifted syngas is cooled in the low temperature gas cooling (LTGC) system by generating low pressure steam, preheating boiler feed water, and heat exchanging against cooling water before going through the acid gas removal system for sulfur removal.
There is some flexibility for locating the WGS reactor: it can be located either before the sulfur removal step (sour shift) or after sulfur removal (sweet shift). Sour shift uses a cobalt-molybdenum catalyst and is normally located after the water scrubber, where syngas is saturated with water at about 450°F to 500°F, depending on the gasification conditions and the amount of high temperature heat recovery. An important benefit of sour shift is its ability to also convert carbonyl sulfide (COS) and other organic sulfur compounds into hydrogen sulfide (H2S) to make downstream sulfur removal easier. Therefore, syngas treated through WGS does not need separate COS hydrolysis conditioning.
A conventional high temperature (HT) sweet shifting operates between 550°F to 900°F and uses chromium or copper promoted iron-based catalysts. Because syngas from the sulfur removal process is saturated with water at either near or below ambient temperature, steam injection or other means to add moisture to the feed is normally needed for HT sweet shifting.
A conventional low temperature (LT) sweet shift, typically used to reduce residual CO content to below 1%, operates between 400°F to 500°F and uses a copper-zinc-aluminum catalyst. LT sweet shifting catalysts are extremely sensitive to sulfur and chloride poisoning and are normally not used in coal gasification plants.
Sweet shift is normally not used for coal gasification applications, given the problems of sulfur and chloride poisoning as mentioned above, in addition to the inefficiency of having to cool the syngas before sulfur removal, which condenses out all of the moisture gained in the water scrubber, and then reheating and re-injecting the steam into the treated gas after H2S removal to provide moisture for shift. Sour shift is normally preferred for coal gasification applications since the moisture gained in the water scrubber is used to drive the shift reaction to meet the required H2/CO ratio.
Hydrogen Production
As explained above, water gas shift is commonly used to adjust H2 to CO ratios in syngas for many end products or purposes of coal gasification. However, in the production of hydrogen it is an essential post-gasification operation and used to convert all CO present in the syngas to CO2, yielding the maximum possible amount of hydrogen. The principles of shift reactions, catalysts used, and reactor setups are the same as discussed above but with an emphasis of process configurations to take the shift reaction to a complete extent. Discussion on hydrogen production from coal contains descriptions of process arrangements to generate hydrogen as a primary product or coproduct from coal.
The 10 largest coal producers and exporters in Indonesia:
Sponsor Ads
Created on Jul 12th 2019 07:52. Viewed 693 times.
Comments
No comment, be the first to comment.