Bearing and sleeve machining technology introduction
by xiaolong luo cnc machining shopBearing is an important component in contemporary mechanical equipment. Its main function is to support the mechanical rotating body, reduce the friction coefficient during its movement, and ensure its rotation accuracy. Rolling bearings generally consist of an outer ring, an inner ring, a rolling element and a cage. According to the shape of the rolling element, the rolling bearing is divided into two categories: ball bearing and roller bearing.
Although there are many types of rolling machining bearings, their structural types, tolerance grades, material selection, and processing methods are different, but the basic manufacturing process is similar. The following small pellets briefly introduce the processing technology of the bearing parts:
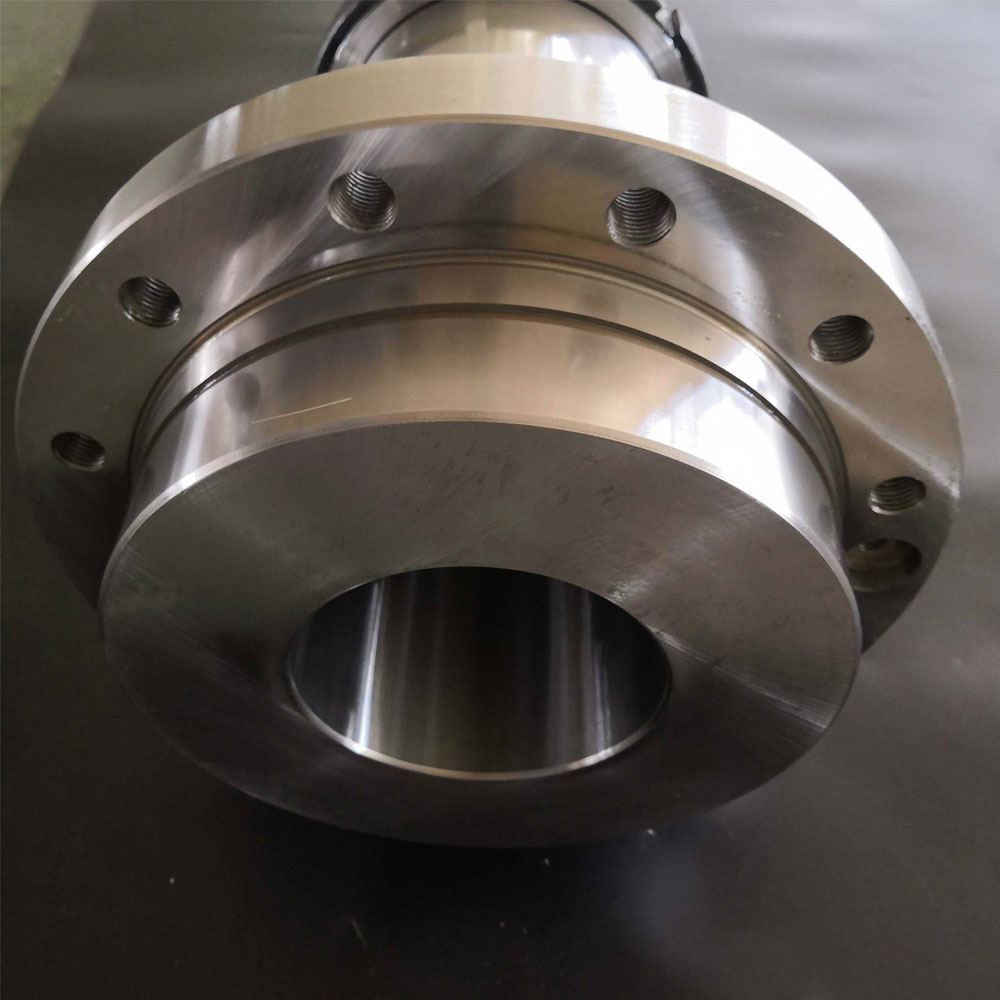
Bearing manufacturing process sequence
(1) Bearing parts manufacturing - bearing parts inspection - bearing parts demagnetization, cleaning, rust - bearing assembly - bearing finished product inspection - bearing finished product demagnetization, cleaning - bearing finished oil coating package finished goods into the warehouse.
(2) The ferrule is an important part of the rolling bearing. Due to the wide variety of rolling bearings, the ferrule size, structure, equipment used and manufacturing methods of different types of bearings are different. Moreover, due to the many processing steps of the ferrule, complicated process and high processing precision, the processing quality of the ferrule has an important influence on the accuracy, service life and performance of the bearing.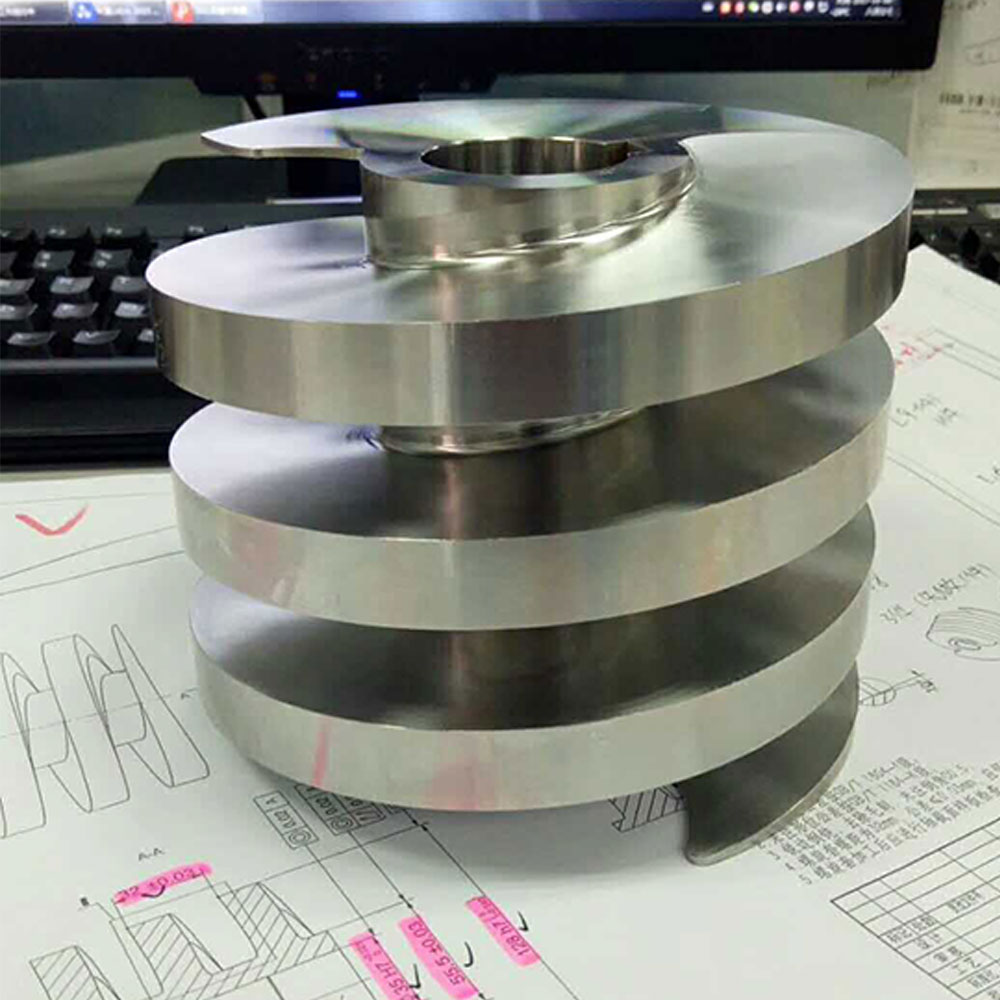
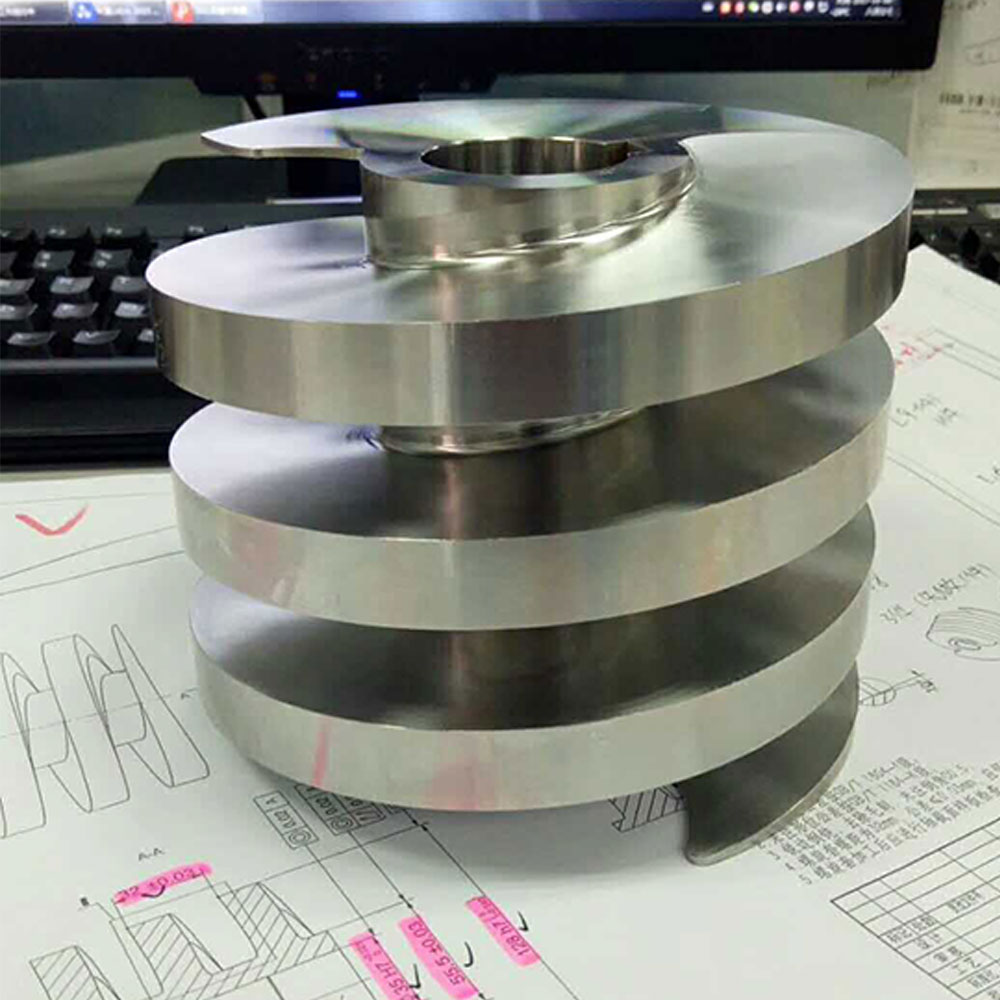
Bearing ring process sequence
The raw material for the manufacture of the ferrule is a cylindrical bar or tube. At present, depending on the molding process, the rolling bearing ferrule generally has the following manufacturing processes.
(1) Bar stock: blanking-forging-annealing (or normalizing)-turning (cold press forming)-heat treatment quenching, tempering-grinding-part inspection-demagnetization, cleaning-submission assembly.
(2) Bar material, pipe material: blanking - cold head forming - heat treatment quenching, tempering - grinding - parts inspection - demagnetization, cleaning - submission assembly.
(3) Pipe material: blanking-turning forming-heat treatment quenching, tempering-grinding-part inspection-demagnetization, cleaning-submission assembly
(4) Bar stock: blanking-cold (warm) extrusion molding-turning-heat treatment quenching, tempering-grinding-part inspection-demagnetization, cleaning-submission assembly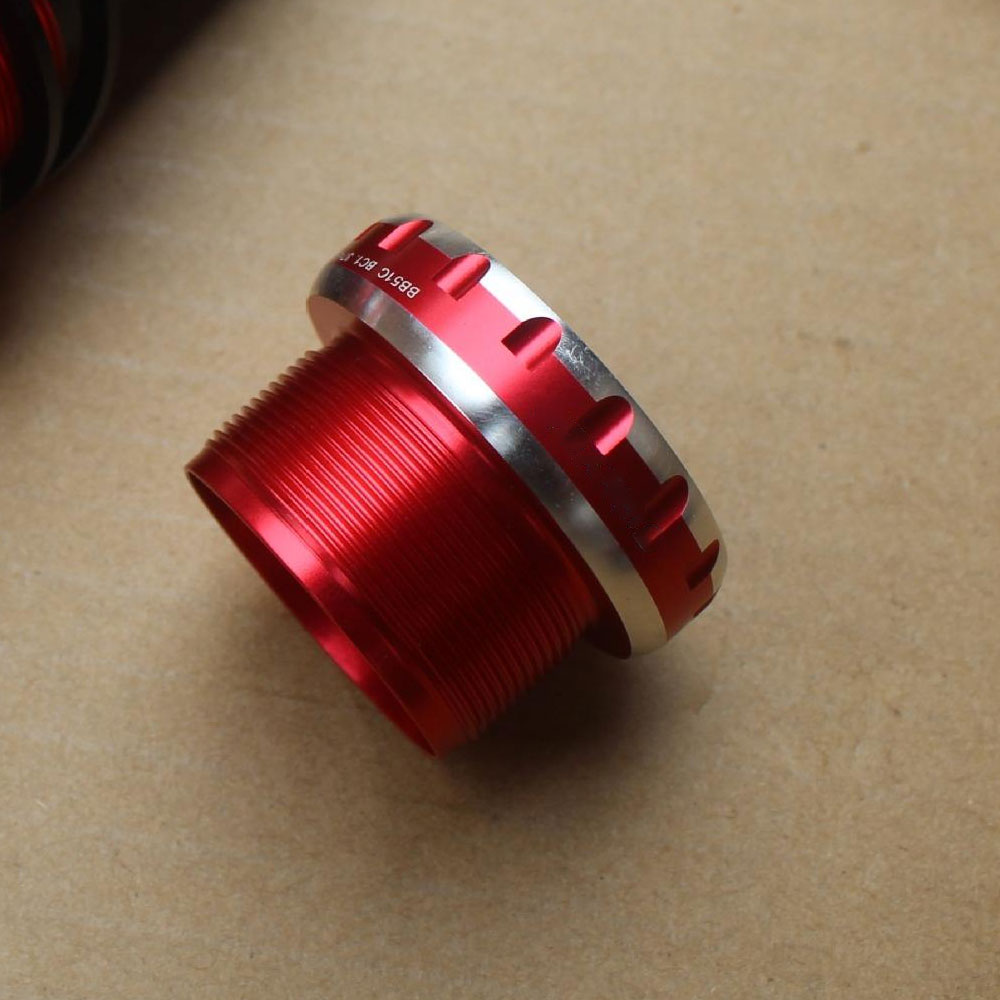
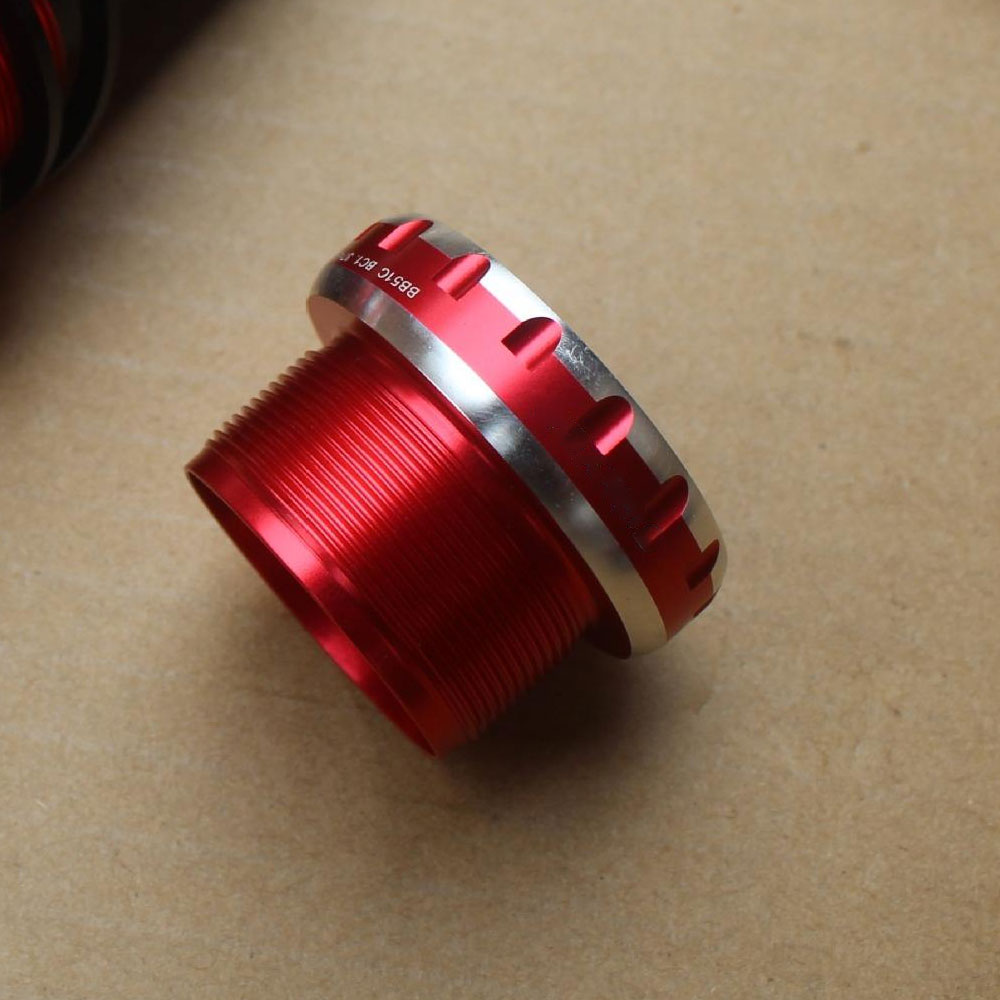
Ferrule forming method
At present, there are mainly the following molding methods in the ferrule processing: forging type, turning forming, cold boring expansion molding and cold (warming) extrusion molding.
(1) Forging type can eliminate metal internal defects by forging processing, improve metal structure, make metal flow line distribution reasonable, and metal tightness. Forging-type processing technology is widely used in bearing forming processing. Common forging methods include hot forging, cold forging and warm forging.
(2) The stamping forming process is an advanced process method that can improve the material utilization rate, improve the compactness of the metal structure, and maintain the linearity of the metal flow. It is a chipless processing method. When using the stamping process and the forging type process, the accuracy of the product is affected by the precision of the molding die, in addition to the accuracy of the molding die.
(3) The traditional turning forming technology uses a special lathe to complete the forming process using a centralized process. Some products with complex shapes and high precision requirements are increasingly using CNC turning technology.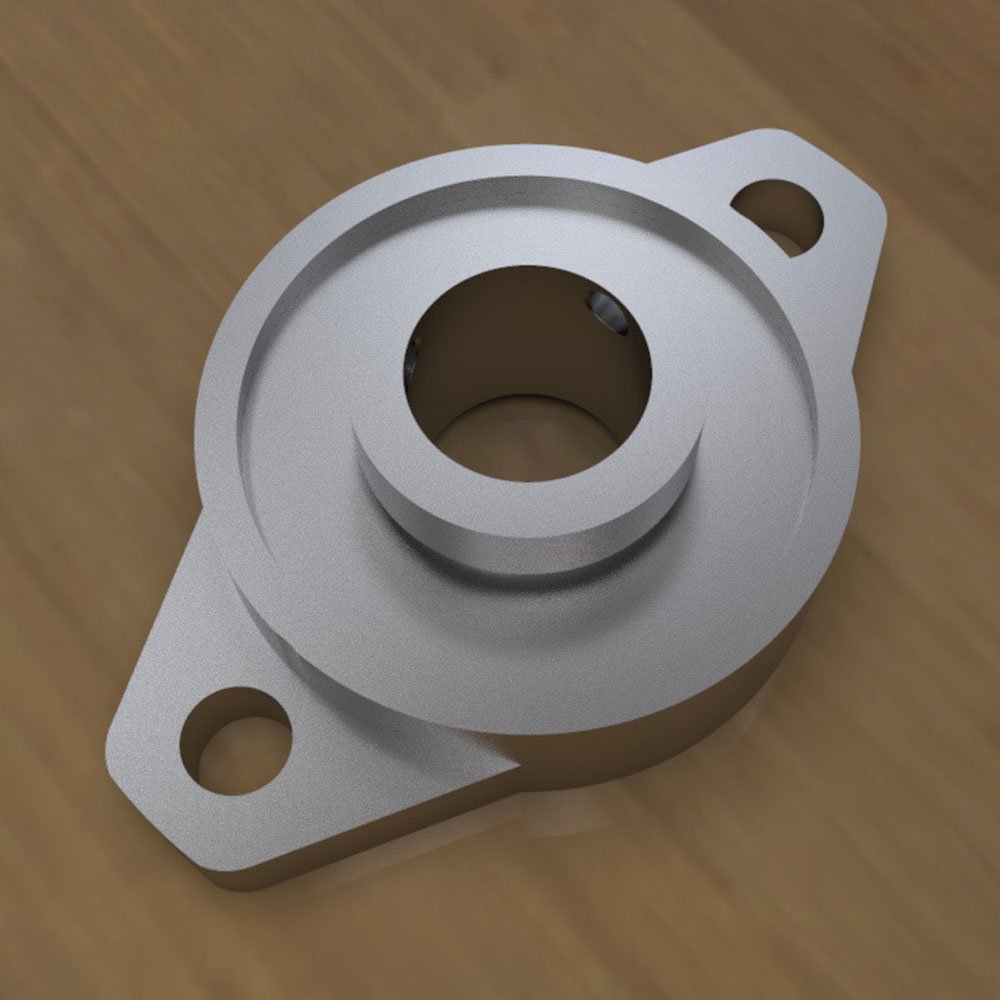
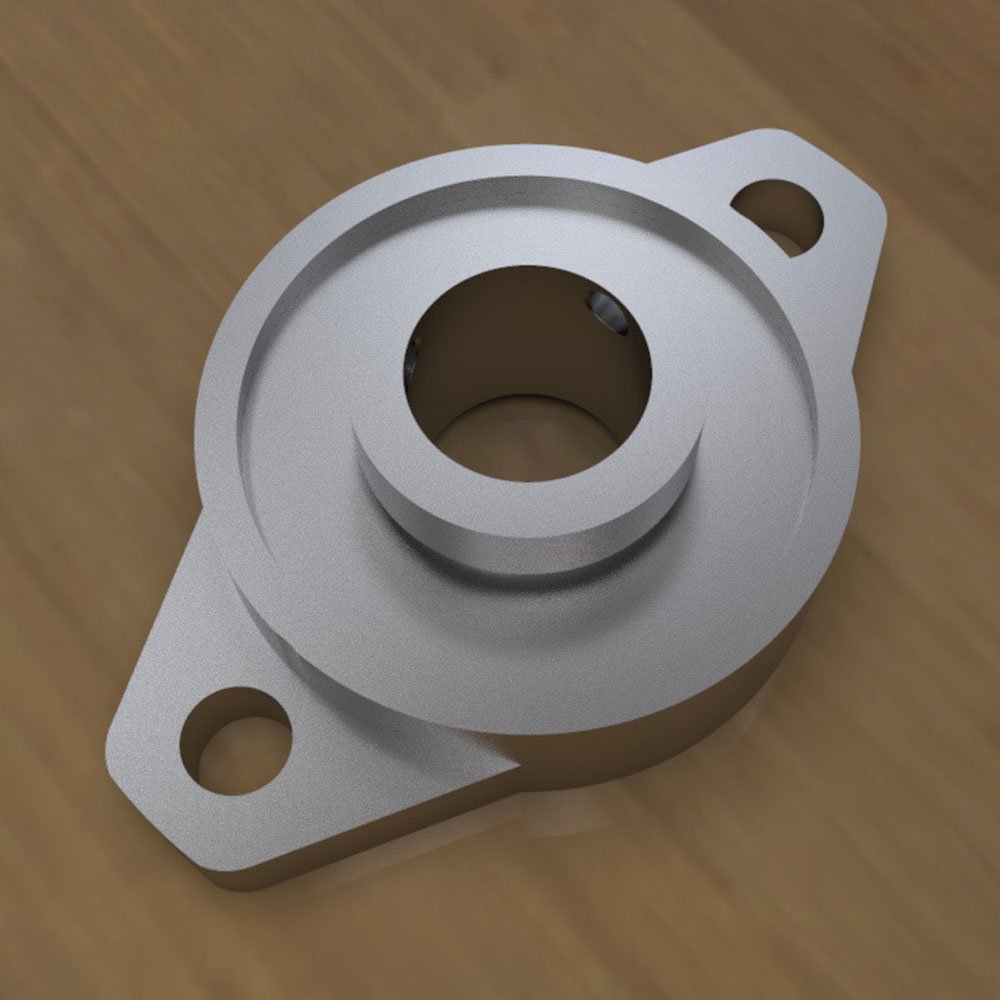
Bearing processing oil selection
In addition to the hot forging process, the bearing fittings usually use suitable metalworking oils according to the process to improve workpiece accuracy and processing efficiency.
(1) Cold forging: Most of the cold forming oil or strong shrinking oil is used to improve the precision of the workpiece.
(2) Stamping: Since the stamping process is limited by the precision of the mold, special stamping oil is used to extend the service life of the mold to ensure the accuracy of the workpiece.
(3) Turning: The precision of the turning process is mainly related to the feed speed and tool strength of the cutting art. The special lathe cutting oil can effectively reduce the cutting temperature and prevent the occurrence of thermal deformation.
The above is a brief introduction to the processing technology of bearing rings. Bearing processing is developing in the direction of high utilization rate of metal materials, high production efficiency and high molding precision.
PTJ Shop Supply Bearing Services vision is to provide our customers with the highest level of satisfaction imaginable by offering them innovative solutions, cultivating long term relationships, anticipating their future needs.
Sponsor Ads
Created on Nov 21st 2019 19:47. Viewed 263 times.
Comments
No comment, be the first to comment.