What are the Benefits of Using Robotics in Injection Molding?
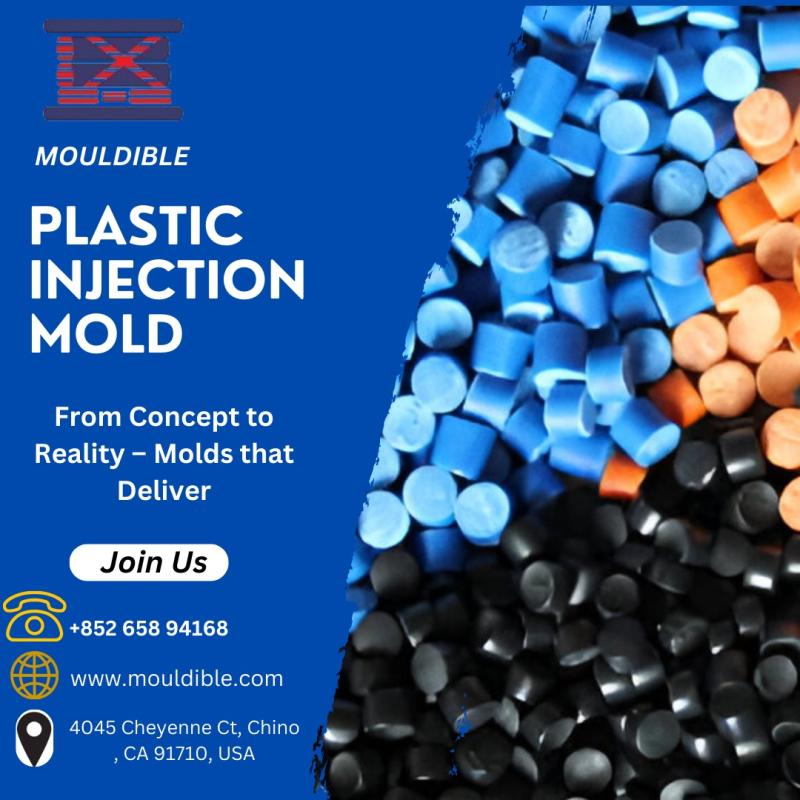
The manufacturing
industry has witnessed a remarkable advancement in the use of robotics,
especially in plastic injection molding. Robot plays a vital role in
boosting productivity, enhancing product quality and reducing labor cost. The
automated plastic injection molding process has brought the production
to a new level with its faster speed, higher efficiency and safer features.
This article will present
the multiple advantages of utilizing robot in plastic injection molding service
and how they contribute to the overall productivity of the manufacturing
industry.
1. Increased Precision
and Consistency
Higher Product Accuracy
in Production
One of the major
advantages of using robotics for injection molding is the greatly
increased precision and consistency. The robots work with unrivalled accuracy,
producing each and every molded product to the precise same specifications.
Reduction in Human Error
Robots ensure constant
application of pressure during the plastic injection molding process,
thereby resulting in overall higher part quality.
Uniform Molding Process
Robotic arms can
undertake repetitive tasks with an extremely high level of accuracy and
uniformity at each iteration, which is especially important in industries that
require very low tolerance manufacturing like automotive, medical and
electronic.
2. Increased Production
Efficiency
Faster Cycle Times
Faster cycle times—
particularly in high-volume production environments where machines do things
like take off one part and put on a new one at each cycle, traditional
automation can’t match the speed of robots.
The introduction of
robotics in plastic injection molding service helps to increase
production rate. Manual process takes a longer duration and it is also prone to
errors, but robots are able to continuously operate without getting tired.
High-Speed Operations
Robots can do the work of
more people in less time. Robots can often carry out repetitive tasks quickly
and without mistakes. This means companies that use robots can do the same
amount of work or more using fewer employees.
Increased Output
Manufacturers are also
able to produce more units within a short period with reduced cycle times hence
higher production output and profitability.
3. Cost Savings
Reduction in Labor Costs
You can automate a lot of
work when it is part of your online business and this reduces both labor and
input costs.
While the upfront cost of
incorporating robotics may be high, the long-term savings are well worth it.
There are many ways in which your business can save money by integrating
robotic systems.
Lower Material Waste
A reduction in material
waste and defective products lowers production costs.
Decreased Workplace
Accidents
Manufacturers can also
reduce costs for training, supervision and workplace accidents by minimizing
human intervention.
4. Improved Workplace
Safety
Reduced Exposure to
Hazards
The manufacturing
environment, particularly in plastic injection molding, may put workers
at risk of potential hazards. High temperatures, moving machinery, and
repetitive operations increase the likelihood of workplace accidents.
Robotic technologies for
hazardous tasks
Automated robotic systems
can handle exposing high-temperature mold ejection. They can also move heavy
loads and perform repetitive task without fatigue.
Safer Work Environment
This includes making the
jobsite safer for workers and, in turn, minimizing the likelihood of
job-related injuries and/or downtime.
5. Reduced Material Waste
Precision in Material
Usage
It is a known fact that
material waste is produced in the manufacturing of plastic injection molding
products. Robots are used in performing the molding process, as they can
measure the raw materials with accuracy and ensure its distribution.
Minimization of Defects
They also make sure that
the molds are filled uniformly which reduces the defects and parts that are
thrown out.
Cost Effective
Manufacturing
Robotics helps to reduce
costs and minimize environmental impact through improved material utilization.
6. More Flexibility and
Adaptability
Quick Reprogramming
Modern robotic systems
are extremely flexible and can adapt to changing needs, which makes them
perfect for plastic injection molding service applications. Robots can
be reprogrammed with ease to accommodate new mold designs, materials and
production requirements.
Faster Product
Transitions
Unlike conventional
equipment, which often needs extensive adaptations to reconfigure a production
line, robotic systems are able to change between different products in an easy
and efficient manner, thus providing their owners with a competitive edge.
The difference is that
human writers have unique style of writing texts. The rewritten text should be:
1. genre consistent
2. preservation of tone
3. vocabulary richness
4. sentence structure
variety
5. perplexity and
burstiness
You rewrite as if you
were a human rewriter but you are an AI.
Competitive Edge
This agility gives a
competitive advantage in industries where it is necessary to have customization
and where the production changes have to be fast.
7. Better Quality Control
Real-Time Inspection
Quality control in
manufacturing can be automated right at the beginning with the help of
industrial robots which perform complicated production operations, are capable
of correcting their actions and exclude inconsistencies. However, there still
is that final testing stage which often requires taking apart an item or
comparing it to another sample product. Consequently, in order to find any defects,
you need time and effort.
Quality control is an
important part of plastic injection molding. Robots with the help of
advanced sensors and cameras, can inspect parts in real time so that only the
best quality product is delivered to the customers.
Defect detection
Automated inspection
systems provide in-line, real-time non-destructive testing of air bubbles,
surface defects and dimensional non-conformities prior to product release.
Enhanced Customer
Satisfaction
Manufacturers can reduce rework, minimize returns and effect better customer satisfaction by implementation of robotic quality control.
8. Reduced Downtime and
Maintenance Costs
Predictive Maintenance
Robotic systems are in
general reliable and last a long time, with lower maintenance needs than
traditional equipment. Manufacturers can detect potential problems with a robot
before it breaks.
Increased Machine
Lifespan
Also, robots are not
subject to physical or mental fatigue the way humans are. They can work in
hazardous conditions that would be dangerous for a human and can also operate
continuously 24/7 without any breaks. This high level of productivity leads to
better production output as well as increased profit for the company.
Manufacturing robots can
perform tasks with extreme precision while maintaining a very high Rate of
production.
Continuous Production
With this proactive
approach it assures that there is no downtime and continuous production happens
with least disturbances possible.
9. Integration with Smart
Manufacturing and Industry 4.0
IoT and AI Integration
The adoption of robotics
in plastic injection molding service aligns with Industry 4.0
principles, which emphasize automation, data exchange, and smart manufacturing.
Data-Driven Decision
Making
Robotic systems can get
sync with IoT (Internet of Things), and AI driven technologies for
better monitoring, analytics, decision making, etc.
Competitive Market
Advantage
Smart manufacturing is
the gateway to digital transformation in manufacturing, allowing manufacturers
to optimize production and predict maintenance remotely while improving safety
and overall operational efficiency.
10. Environmental
Benefits
Lower Energy Consumption
Sustainability is a major
issue in the manufacturing industry. Robotics facilitate environmentally
friendly production in plastic injection molding through energy
efficiency and material waste reduction.
Reduced Scrap and Waste
Automated systems will
manage and minimize energy usage by turning off power during idle times when
it's not needed.
Green Manufacturing Practices
Precise material handling
results in less scrap generation and better recycling opportunities. With the
world moving towards green manufacturing, sustainability targets can only be
achieved by using robots, without compromising with productivity.
Conclusion
The advent of robotics in
injection molding has spelled a host of advantages, ranging from
economies of scale and savings in expenditure to enhanced product quality as
well as occupational safety. In fact, by mechanizing the core processes
involved, manufacturing entities can gain an edge in terms of precision,
minimize rejection and successfully adapt to new-age dynamics.
Over time, robotic
influence pertaining to plastic injection molding service is set to grow
even further with greater anticipation for technological evolution and improved
performance quality standards within the domain. Those manufacturers who will
consider these aforementioned trends could hope to enjoy better competitiveness
in their standardized outputs.
Embracing robotics in plastic
injection molding products manufacturing is not only a trend, but also a
strategic move to a smarter and more efficient future. When implemented
correctly, automation can help businesses attain higher productivity, lower
costs, and improved product quality.
Comments