An Ultimate Guide to Nitrogen Generator
by Rick Minnuo SEOerWhat is a Nitrogen Generator Used For?
A nitrogen generator is a device used to produce nitrogen gas on-site. It employs physical or chemical methods to separate nitrogen from the air, providing a continuous supply of high purity (up to 99.9995%) nitrogen gas. Using an on-site nitrogen generator not only alleviates concerns about nitrogen supply but also helps save on transportation and storage costs for nitrogen.
Why Do We Need Nitrogen?
Nitrogen is a colorless, odorless gas that makes up a significant portion of the air (comprising 78.08% of the earth’s atmosphere by volume). With an extremely low boiling point, it only liquefies into a liquid form at temperatures below -195.8 degrees Celsius. Its remarkable chemical stability and resistance to reacting with other substances make it a valuable resource in modern industry. The semiconductor industry, metalworking, food preservation, pharmaceuticals, and even aerospace all require significant amounts of nitrogen. To ensure a stable supply of high-purity nitrogen, nitrogen generators have become indispensable. This article will provide a comprehensive overview of everything you need to know about nitrogen generators.
How Does a Nitrogen Generator Work?
Initially, nitrogen gas was produced in large quantities using chemical methods, a process known as cryogenic distillation. This involved first cooling air to liquefy it, followed by heating it to separate its components based on their different boiling points. However, this method required substantial investment and infrastructure, making it impractical for on-site small-scale nitrogen production. It wasn’t until the mid-20th century that pressure swing adsorption technology allowed for the widespread application of small-scale nitrogen generators. Concurrently, membrane separation emerged as an alternative method, enabling energy-efficient nitrogen production. Below, I will provide an overview of how mainstream nitrogen generation equipment generally operates.
Pressure Swing Adsorption (PSA)
Pressure Swing Adsorption technology is a nitrogen production process that separates oxygen and nitrogen based on the differing adsorption efficiency of molecular sieves for these gases. Molecular sieves are a special type of adsorbent. Their pore size and structure allow them to “capture” molecules of specific sizes and shapes, achieving the separation of gases. Taking common carbon molecular sieves as an example, they exhibit different adsorption rates for oxygen and nitrogen. The smaller volume oxygen molecules have a faster diffusion rate, allowing the carbon molecular sieves to adsorb oxygen more rapidly. Consequently, when we shorten the adsorption time to an appropriate duration (usually around 1 minute), most oxygen molecules are adsorbed, leaving mostly nitrogen. By repeating this process, we can obtain nitrogen with a purity level of up to 99.999%. Simultaneously, applying and releasing pressure affects the adsorptive capacity of the molecular sieve, and creating a pressure difference allows the saturated molecular sieve to undergo desorption. Therefore, by using multiple adsorption towers to carry out the adsorption and desorption processes simultaneously, we can achieve continuous production of nitrogen gas.
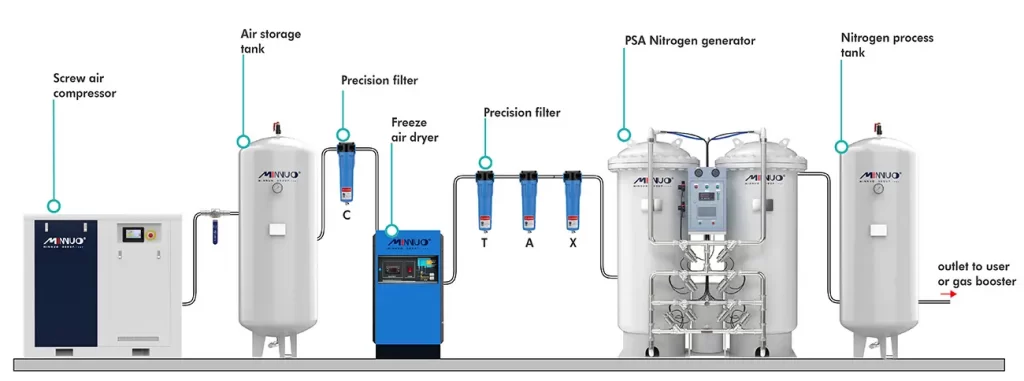
Cryogenic Air Separation
Cryogenic air separation is a traditional method for nitrogen production. In this process, air is first cooled to the point of liquefaction, resulting in primarily liquid oxygen and liquid nitrogen. Due to the different boiling points of liquid nitrogen and oxygen, they are separated during the subsequent distillation process. Cryogenic air separation can produce nitrogen with a purity level exceeding 99.999%. Additionally, this method can also produce liquid nitrogen.
Membrane Separation
In contrast to PSA technology, membrane separation doesn’t utilize molecular sieves to separate gases; instead, it employs a specialized polymer membrane. As mixed gases pass through the membrane, their differing solubilities and diffusion coefficients cause them to move through the membrane at different rates. Consequently, gases with faster permeation rates enrich on one side of the membrane, while gases with slower permeation rates remain on the original side. Unlike molecular sieves, there is no requirement for pressurizing or cooling the membrane, making membrane separation technology more energy-efficient. A membrane nitrogen generator can directly produce nitrogen with a purity of 99.5%, but additional purification equipment is often necessary for applications requiring higher-purity nitrogen.
Components of a Nitrogen Generator
A nitrogen generator based on Pressure Swing Adsorption (PSA) technology typically comprises the following components:
- Air Compressor: Compresses air to a certain pressure before entering the system.
- Air Purification Unit: Consists of multiple filters to remove impurities such as water vapor and carbon dioxide.
- Adsorption Towers: The core component of a PSA nitrogen generator is the cylindrical adsorption tower. Typically, two adsorption towers operate in a cycle. When one tower becomes saturated, the control system automatically switches to the other tower, allowing the adsorbent in the first tower to regenerate. This cycle ensures a continuous supply of nitrogen.
- Purification Unit: Nitrogen undergoes further purification here through methods such as heating or creating a pressure difference to achieve the desired purity.
- Nitrogen Storage Tank: Used to store the on-site produced nitrogen.
- Control System: Manages the automatic operation of the entire nitrogen generation system. This includes PLC controllers, touchscreens, sensors, and more.
The process and components of a membrane nitrogen generator are similar to a PSA nitrogen generator, with the difference being the use of a polymer membrane for gas separation.
Similarly, the cryogenic nitrogen generation process requires pre-compression and purification steps. Its core components include an air separation unit, commonly comprised of a main heat exchanger, liquefier, distillation column, condenser, and evaporator.
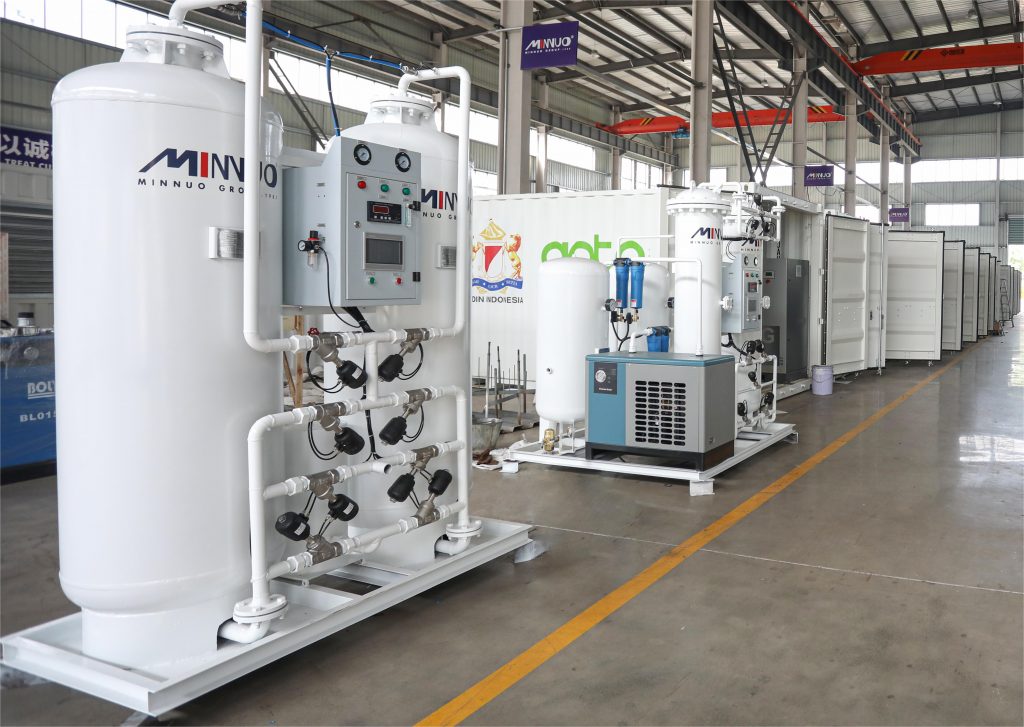
What Purity of Nitrogen Do I Need?
Typically, nitrogen with a purity between 90% and 99.9% is considered low purity. Nitrogen with a purity of 99.998% is considered high purity, while ultra-high purity generally refers to nitrogen with a purity of 99.999%, with almost no impurities. Different applications have vastly different requirements for nitrogen concentration. The purity of nitrogen you require usually depends on how impurities in the nitrogen will affect your process. Different applications have varying sensitivity to moisture, oxygen, and other impurities.
Chemical Industry
In the chemical industry, nitrogen is often used as a feed gas or for pipeline purging and atmosphere creation. The chemical industry typically requires nitrogen with a purity of no less than 98%.
Electronics and Semiconductor Industry
For electronics manufacturing and the semiconductor industry, nitrogen purity typically ranges from 99.99% to 99.999%. Lower concentrations of nitrogen can be used for simple processes such as part cleaning.
Food-Grade Nitrogen
Nitrogen used in food and beverage production is generally used to prevent oxidation and preserve flavor. The purity requirements for food-grade nitrogen typically range from 98% to 99.5%.
Pharmaceuticals
High-purity nitrogen is required in the pharmaceutical production process to prevent product contamination. The manufacture of many drugs requires high-purity nitrogen of 99.99%.
Metallurgy and Metalworking
Nitrogen is widely used in metallurgical processes such as annealing and sintering. Different metalworking processes have varying purity requirements for nitrogen. For instance, heat treatment may require a purity of 95-99%, while laser cutting may require high-quality nitrogen with a purity as high as 99.999%.
On-Site Nitrogen Generation or Cylinder Purchase: What’s the Better Option?
Undoubtedly, before choosing nitrogen generation equipment, you might ask: “Why not just buy bottled nitrogen gas?” I’ll tell you the factors to consider when making this decision.
In the short term, bottled nitrogen gas has cost advantages. However, in the long term, nitrogen generation equipment will have a clear cost advantage in terms of the cost per cubic foot of nitrogen gas.
You need to consider your gas usage. Bottled nitrogen gas is suitable for small-scale users; you need to evaluate the scale of your business and whether you need to expand production.
Moving nitrogen cylinders requires a significant amount of manpower and takes up a large amount of your storage space. Moreover, in situations requiring continuous gas supply, cylinders are far less convenient than nitrogen generation equipment.
Of course, nitrogen generation equipment is not always the optimal solution. It requires regular maintenance and will consume a certain amount of initial investment.
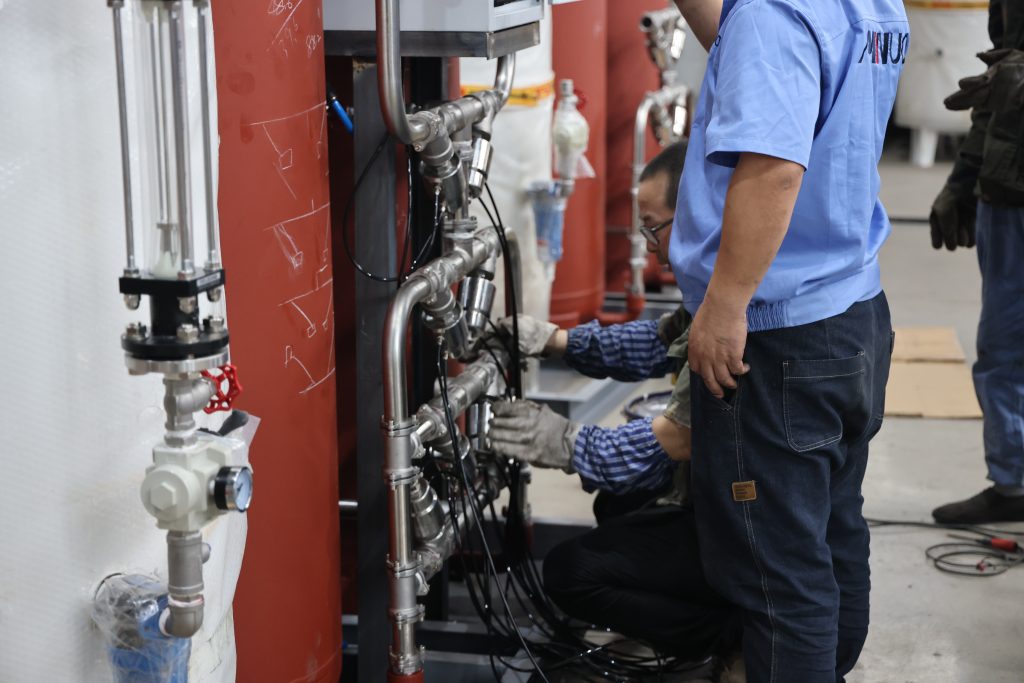
How to Choose a Nitrogen Generator
Regardless of the type of nitrogen generator you need, it’s essential to convey the following parameters to the manufacturer. Trust me, providing this information will enable them to offer you the most suitable solution:
Nitrogen Purity:
Determine the appropriate purity based on the requirements of your industry and processes. The right purity level will ensure the quality of your products. Typically, membrane separation technology is suitable for lower purity requirements, while PSA technology and cryogenic air separation can achieve higher purities.
Nitrogen Flow Rate:
This refers to your usage. It is commonly measured in Nm³/h or NL/min, with “N” denoting standard conditions of 20°C and standard atmospheric pressure. Describing your usage is crucial for the selection process. In general, cryogenic systems are suitable for large-scale industrial nitrogen production, while PSA and membrane technologies are more economical for medium to small-scale applications.
Nitrogen Pressure:
The nitrogen pressure will directly impact the flow rate. In general, higher pressure results in greater flow.
Nitrogen Dew Point:
The dew point refers to the temperature at which water vapor in the gas condenses into liquid. It is commonly used to indicate the moisture content in the gas. Typically, the higher the dew point, the higher the moisture content in the gas. Many industrial processes have requirements regarding the moisture content of nitrogen. When nitrogen with excessive moisture comes into contact with the product, it can impact product quality.
By providing these details, the manufacturer can better tailor the nitrogen generator to your specific needs, ensuring efficient and effective nitrogen production for your operations.
Additional Considerations for Purchasing
Costs of Nitrogen Generators
Typically, the cost of a nitrogen generator comprises several aspects: equipment investment, electricity consumption, and equipment maintenance.
- Equipment Investment: This depends on your nitrogen usage and purity requirements. Generally, for large-scale industrial nitrogen production, cryogenic air separation offers the best cost-effectiveness. In medium to small-scale applications, membrane nitrogen generators have a higher initial price but consume less energy and require less maintenance compared to PSA nitrogen generators.
- Electricity Consumption: The air compressor accounts for the majority of the power used in the entire nitrogen generation system. Larger nitrogen flow rates require more compressed air, resulting in higher electricity consumption.
- Maintenance: Typically, the oil and oil filter cartridges need replacement every 2000 hours, while the air filter cartridges need replacement every 4000 hours.
Optimizing Production Efficiency
Unlike bottled nitrogen gas, nitrogen generation equipment requires prudent use to achieve optimal production efficiency and minimize costs. Here are some pieces of advice:
- Adhere to operating procedures and safety regulations. Always remain attentive to changes in equipment parameters to prevent equipment failures and accidents caused by excessive pressure.
- Perform regular cleaning and maintenance.
- Schedule operating times sensibly. This not only avoids unnecessary energy waste but is also meaningful for prolonging the lifespan of the nitrogen generator.
- Optimize the working environment. Temperature and humidity significantly affect the operation of nitrogen generators. Avoid running the nitrogen generator in high-temperature and high-humidity environments. Moreover, optimizing equipment layout is positive for reducing energy consumption and increasing production output.
How to Obtain Liquid Nitrogen
Liquid nitrogen can be obtained by cooling the nitrogen gas produced by a nitrogen generator to its liquefaction temperature. Therefore, industrial liquid nitrogen generators typically involve the addition of nitrogen compression equipment and a refrigeration unit to the nitrogen generation system. It is important to note that liquid nitrogen is typically used through vaporization, requiring specialized storage and vaporization equipment. Additionally, obtaining a specialized equipment registration certificate that complies with the requirements of your country is necessary. Furthermore, the performance of liquid nitrogen does not differ, so for users requiring low-purity nitrogen, it may not be cost-effective.
Alternative
When you opt not to generate nitrogen on-site, obtaining pre-made nitrogen externally is practically your only option. Common alternatives to on-site nitrogen generation include nitrogen cylinders, liquid nitrogen dewars, and liquid nitrogen bulk tanks. Of course, using these alternatives is not without its costs: pressurized nitrogen cylinders pose safety hazards during transportation and storage, and may also cause mechanical injuries when in use. Additionally, there is always a certain amount of residual gas in cylinders, leading to inevitable waste. Disruptions in the supply chain can also lead to production downtime. Liquid nitrogen dewars present similar challenges. Meanwhile, liquid nitrogen bulk tanks transported over long distances by tanker trucks will occupy a considerable amount of space and may not be suitable for all applications.
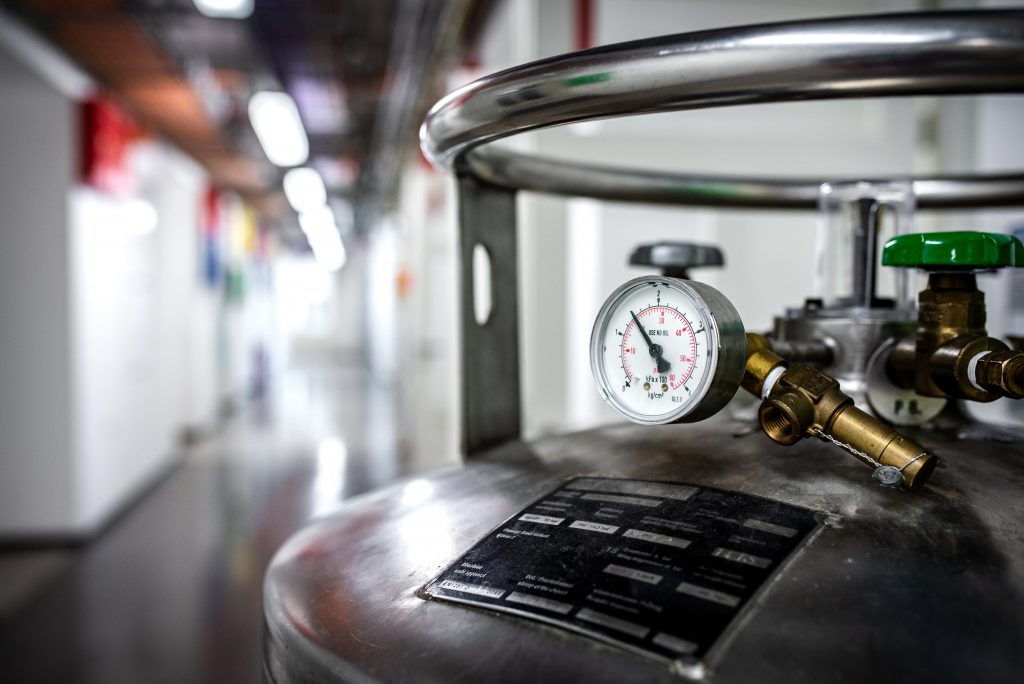
Conclusion
In summary, within the current scope, there haven’t been significant changes in the large-scale acquisition of nitrogen. Therefore, the future direction of nitrogen generator development will still focus on improving gas separation efficiency, enhancing miniaturization capabilities, and environmental friendliness. For more information on nitrogen generators, please visit our homepage.
Sponsor Ads
Created on May 18th 2024 01:01. Viewed 70 times.