When & Why You Should Use PID Autotune?
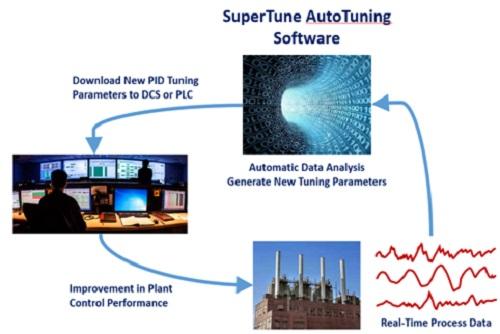
To help determine the best settings of a heating element system, you need to use the PID technology. Yes, by using the knowledge about PID control theory, you can achieve your goal efficiently.
The process is called PID autotune. It’s the practice of using PID feedback loops to adjust PID parameters in PID controllers dynamically. PID autotuning for academic purposes can be performed on any system with a controllable parameter or set of controllable parameters. Such systems are everywhere around us.
They are ubiquitous, which means almost everyone sees them very often but might not have thought about how they work. The most common example is probably heating. To heat something, you need to apply energy somehow. (Credit Information: PiControl Solutions LLC)
About PID Autotune
PID control theory has been around since the 1800s, but PID autotune didn't exist until much later.
In modern times, autotuning through PID has become very relevant because every device now has embedded PID controllers that require PID parameters to be tuned appropriately for optimal operation at all times.
In recent years, this need is only becoming more relevant as PID controllers are getting more complex. PID controller code is found in everything from washing machines to autopilot systems.
Autotune through PID is also of increasing interest for academic research because it provides a general framework for investigating dynamic systems of all kinds. Many real-world problems can be modeled as PID systems, and the autotune system gives insight into the relationship between parameters of control loops and their performance characteristics.
However, PID autotuning can only take place when a system has access to both its own internals and the external environment through suitable sensors. For instance, there must be sensors available that can inform the PID controller about whether or not it needs to change any parameters at any given moment.
A sensor known as a process variable sensor might be used. The PID controller can then measure the process variable to compare it with a set point, which is the regulation value held in the PID controller's memory.
PID control theory provides mathematically optimal PID parameter values, which will result in an output that closely matches this set-point, under certain assumptions about how much time has elapsed since the PID parameters were last changed.
If it turns out that PID Autotuning is necessary, there are three principle options for actually performing the autotune process: Manual Tuning, Automatic Tuning, and Semi-Automatic Tuning.
Each of these has its own pros and cons. There are also hybrid methods which are combinations of any or all of the techniques listed above.
The simplest way to perform autotune is by hand, through trial and error. This method is suitable for PIDs, which are linear functions of PID parameters. If autotuning is non-trivial, trying all the possible tuning steps manually might take too much time.
Another option to autotune would be to use an automated PID Tuner. This program can run PID autotuning algorithms to find optimal PID parameter values in a given system. As this process requires computationally expensive calculations, it's not feasible on embedded systems with limited resources or when there isn't enough processing power available.
The last basic way to perform autotuning without using any external tools would be semi-automatic tuning - where a human PID engineer guides the autotune algorithm but then needs to set PID parameters by hand.
This is the most flexible way of autotuning. However, it might be time-consuming and impractical if rapid PID parameter changes are necessary to keep the system in its optimal state.
Benefits Of Autotuning PID
Autotuning PID provides numerous benefits for control systems engineers and developers, such as:
- Improved PID parameter values (usually) result in improved system behavior. But autotune doesn’t always work! For example, autotuning could lead to a degraded system state.
- PID Tuning can be used to automate tasks that would otherwise require human intervention.
- PID tuning requires no prior knowledge of the system. Therefore it is particularly useful when there isn't enough theoretical information available about the movement patterns of a flying platform or an autonomous car.
Is PID Autotune Worth It?
To put it simply, yes, it’s worth it. Autotuning through PID is appropriate for systems that require PID parameters to be optimized and where PID parameter changes can occur quickly and repeatedly.
- PID control loops: PID controllers are typically used in many automated processes that involve regulating a process variable within a defined range. Typical examples include robotics, aerospace controls, and general manufacturing.
Once autotuning has been implemented, it's possible to monitor system variables and PID parameters in real-time, and PID tuning will always be just a few keystrokes away.
The Bottom Line
PID Autotune can give PID controllers much more flexibility than they would otherwise have. This is particularly true if the PID loop is the central controller for a dynamic system. PID autotuning could allow PID parameters to adapt quickly enough to maintain control over the system’s dynamics.
It provides more options through which an engineer or developer can improve their existing PID parameter values.
Comments